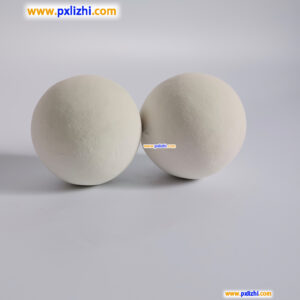
# Inert Ceramic Ball Applications and Benefits
What Are Inert Ceramic Balls?
Inert ceramic balls are spherical, non-reactive ceramic materials used primarily as catalyst supports or tower packing in various industrial processes. These high-quality ceramic balls are manufactured from chemically stable materials like alumina, zirconia, or silica, making them resistant to corrosion and thermal shock.
Key Applications of Inert Ceramic Balls
1. Chemical Processing Industry
Inert ceramic balls serve as excellent catalyst supports in petrochemical plants, oil refineries, and gas processing facilities. They provide a stable surface for catalysts while withstanding harsh chemical environments and high temperatures.
Keyword: inert ceramic ball
2. Environmental Protection
These ceramic balls are widely used in air pollution control systems and wastewater treatment plants. Their high surface area and chemical stability make them ideal for scrubbing processes that remove pollutants from industrial emissions.
3. Petroleum Refining
In the petroleum industry, inert ceramic balls are used in reactors and fractionating towers to improve vapor-liquid contact and enhance separation efficiency during crude oil processing.
4. Fertilizer Production
Ammonia and urea manufacturing plants utilize inert ceramic balls in their synthesis converters to support catalysts and maintain proper gas distribution throughout the reaction chambers.
Benefits of Using Inert Ceramic Balls
1. Exceptional Thermal Stability
These ceramic balls can withstand extreme temperatures up to 1600°C (2912°F) without losing their structural integrity, making them suitable for high-temperature applications.
2. Chemical Inertness
Their non-reactive nature ensures they don’t contaminate processes or react with the materials they come in contact with, maintaining process purity.
3. High Mechanical Strength
Inert ceramic balls offer excellent resistance to crushing and abrasion, ensuring long service life even in demanding industrial environments.
4. Improved Process Efficiency
Their uniform size and spherical shape promote better fluid distribution and contact, leading to more efficient chemical reactions and separations.
5. Cost-Effectiveness
Compared to metal alternatives, inert ceramic balls provide superior performance at lower costs, with reduced maintenance requirements and longer replacement intervals.
Choosing the Right Inert Ceramic Balls
When selecting inert ceramic balls for your application, consider factors such as:
- Chemical composition requirements
- Operating temperature range
- Pressure conditions
- Required size and surface area
- Specific gravity needs
- Crush strength specifications
Proper selection ensures optimal performance and longevity in your specific industrial process.