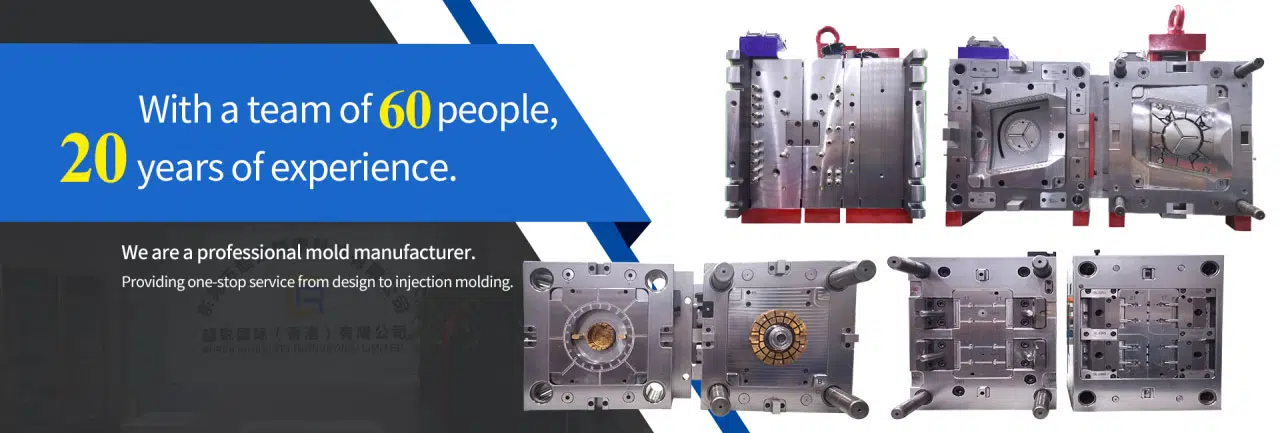
# Sheet Metal Fabrication Techniques and Applications
## Introduction to Sheet Metal Fabrication
Sheet metal fabrication is a versatile manufacturing process that transforms flat metal sheets into various shapes and structures. This technique plays a crucial role in numerous industries, from automotive to aerospace, construction to electronics. The process involves cutting, bending, and assembling metal sheets to create functional components or decorative elements.
## Common Sheet Metal Fabrication Techniques
### 1. Cutting
Cutting is the fundamental first step in sheet metal fabrication. Modern techniques include:
– Laser cutting: Uses high-powered lasers for precise cuts
– Water jet cutting: Employs high-pressure water mixed with abrasives
– Plasma cutting: Utilizes ionized gas for cutting thicker materials
– Shearing: Mechanical cutting with blades for straight cuts
### 2. Bending and Forming
After cutting, metal sheets often require shaping:
– Press brake forming: Uses a punch and die to create precise bends
– Roll forming: Continuously bends metal through a series of rollers
– Stamping: Creates complex shapes with dies and punches
– Deep drawing: Forms sheet metal into hollow shapes
### 3. Joining Techniques
Various methods connect fabricated pieces:
– Welding: Fuses metal pieces together using heat
– Riveting: Mechanical fastening with metal pins
– Adhesive bonding: Uses specialized industrial adhesives
– Soldering and brazing: Lower-temperature joining methods
## Materials Used in Sheet Metal Fabrication
The choice of material depends on application requirements:
Material | Properties | Common Applications
Stainless Steel | Corrosion-resistant, durable | Food processing, medical equipment
Keyword: Sheet Metal Fabrication
Aluminum | Lightweight, corrosion-resistant | Aerospace, automotive
Copper | Excellent conductivity | Electrical components
Brass | Decorative, antimicrobial | Architectural elements
Mild Steel | Cost-effective, strong | Structural components
## Applications of Sheet Metal Fabrication
### Industrial Applications
– Automotive components (body panels, frames)
– Aerospace parts (aircraft skins, structural elements)
– HVAC systems (ductwork, vents)
– Industrial machinery enclosures
### Consumer Products
– Appliance housings (refrigerators, ovens)
– Electronics enclosures (computers, servers)
– Furniture components
– Lighting fixtures
### Architectural Uses
– Building facades and roofing
– Decorative metalwork
– Signage and lettering
– Structural support elements
## Advantages of Sheet Metal Fabrication
Sheet metal fabrication offers numerous benefits:
– Cost-effectiveness for medium to high production runs
– High strength-to-weight ratio
– Design flexibility for complex geometries
– Excellent durability and longevity
– Recyclability of materials
– Precision and repeatability in manufacturing
## Future Trends in Sheet Metal Fabrication
The industry continues to evolve with technological advancements:
– Increased automation with robotics
– Integration of AI for process optimization
– Development of new alloys with enhanced properties
– Growth in sustainable fabrication practices
– Advancements in 3D printing for hybrid manufacturing
Sheet metal fabrication remains a cornerstone of modern manufacturing, combining traditional techniques with cutting-edge technology. Its versatility across industries ensures continued relevance as new applications emerge and material science progresses. Understanding these techniques and applications helps businesses make informed decisions about their manufacturing needs.