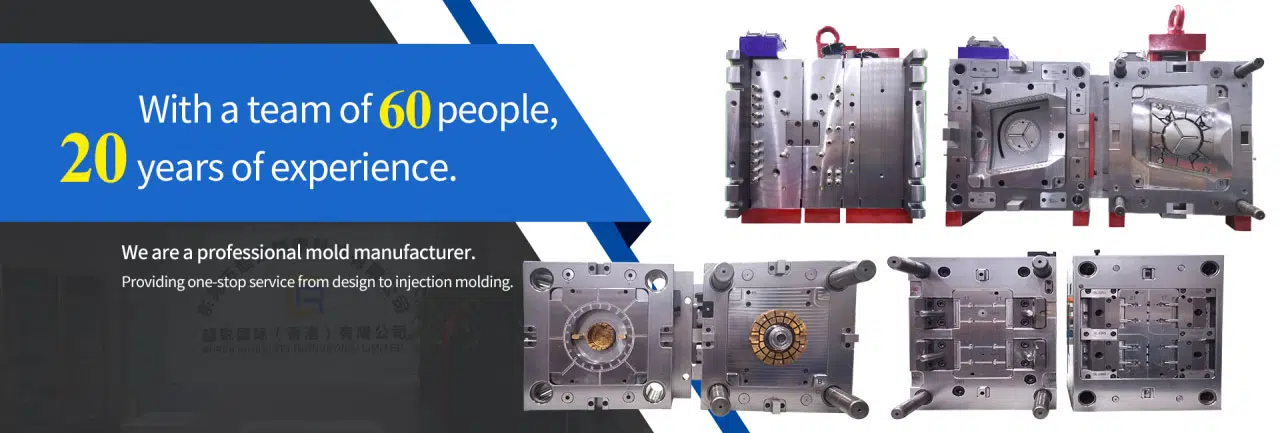
# 5-Axis Machining: Precision and Efficiency in Advanced Manufacturing
## Introduction to 5-Axis Machining
5-axis machining represents a significant leap forward in manufacturing technology, offering unparalleled precision and efficiency for complex part production. Unlike traditional 3-axis machines, 5-axis CNC machines can move cutting tools or workpieces along five different axes simultaneously, enabling manufacturers to create intricate geometries with exceptional accuracy.
## How 5-Axis Machining Works
The five axes in these advanced machines consist of the three linear axes (X, Y, and Z) plus two rotational axes (typically A and B). This configuration allows the cutting tool to approach the workpiece from virtually any direction, eliminating the need for multiple setups and significantly reducing production time.
Key advantages of this movement capability include:
- Ability to machine complex shapes in a single setup
- Improved surface finish quality
- Reduced tool vibration and deflection
- Optimal tool positioning for extended tool life
## Applications Across Industries
5-axis machining has found applications in numerous industries where precision and complex geometries are paramount:
Aerospace
The aerospace industry benefits tremendously from 5-axis capabilities when manufacturing turbine blades, structural components, and other complex aircraft parts that require tight tolerances and intricate shapes.
Medical
Medical device manufacturers use 5-axis machining to create precision implants, surgical instruments, and prosthetics with the required biocompatibility and exacting specifications.
Automotive
Keyword: 5-Axis Machining
High-performance automotive components, including engine parts, transmission components, and custom aftermarket pieces, are increasingly produced using 5-axis technology.
## Benefits Over Traditional Machining
The transition from 3-axis to 5-axis machining offers several compelling advantages:
Reduced Setup Time
By allowing access to five sides of a workpiece in a single setup, 5-axis machines eliminate the need for multiple fixtures and manual repositioning.
Improved Accuracy
With fewer setups comes reduced cumulative error, resulting in parts that meet tighter tolerances and have better overall dimensional accuracy.
Enhanced Surface Finish
The ability to maintain optimal tool orientation relative to the workpiece surface leads to superior surface finishes, often eliminating secondary finishing operations.
Complex Geometry Capability
5-axis machining can produce shapes that would be impossible or prohibitively expensive to make with conventional machining methods.
## Considerations for Implementation
While 5-axis machining offers numerous benefits, there are important factors to consider before implementation:
- Higher initial investment compared to 3-axis machines
- Requires more advanced programming skills
- Necessity for proper operator training
- Workpiece size limitations based on machine envelope
## Future of 5-Axis Machining
As manufacturing demands continue to evolve toward more complex, high-precision components, 5-axis machining is poised to become increasingly prevalent. Advancements in machine design, cutting tools, and CAM software are making this technology more accessible and cost-effective for a wider range of manufacturers.
The integration of automation, IoT capabilities, and artificial intelligence with 5-axis systems promises to further enhance productivity, quality, and operational efficiency in advanced manufacturing environments.