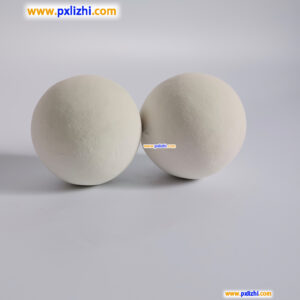
# Inert Ceramic Ball Applications in Industrial Processes
## Introduction to Inert Ceramic Balls
Inert ceramic balls are high-quality, chemically stable ceramic spheres widely used in various industrial applications. These balls are manufactured from premium alumina or other ceramic materials, offering excellent resistance to high temperatures, corrosion, and mechanical stress.
## Key Properties of Inert Ceramic Balls
The effectiveness of inert ceramic balls in industrial processes stems from their unique characteristics:
– High temperature resistance (up to 1600°C)
– Exceptional chemical inertness
– Superior mechanical strength
– Low water absorption
– Excellent thermal shock resistance
– Consistent size and shape
## Major Industrial Applications
### 1. Catalyst Support in Petrochemical Industry
Inert ceramic balls serve as excellent catalyst supports in petroleum refining and petrochemical processing. They provide:
– Uniform distribution of catalyst particles
– Protection against catalyst sintering
– Improved heat transfer
– Reduced pressure drop in reactors
### 2. Packing Material in Chemical Towers
These ceramic balls are extensively used as tower packing in various chemical processes:
– Distillation columns
– Absorption towers
– Stripping columns
– Scrubbers
Their uniform shape and size ensure optimal vapor-liquid contact while minimizing pressure drop.
### 3. Grinding Media in Ball Mills
The high density and wear resistance make inert ceramic balls ideal for:
– Mineral processing
– Cement production
– Paint manufacturing
– Pharmaceutical grinding
### 4. Heat Storage Mediums
In high-temperature heat exchange systems, inert ceramic balls function as:
– Thermal energy storage media
– Heat recovery system components
– Regenerative burner elements
## Specialized Applications
### 1. Environmental Protection
Inert ceramic balls play a crucial role in environmental applications:
– Flue gas desulfurization
– Wastewater treatment
– VOC (Volatile Organic Compounds) removal
### 2. Electronics Industry
Special grades of inert ceramic balls are used in:
– Semiconductor manufacturing
– Electronic component production
– Display panel processing
## Selection Considerations
When choosing inert ceramic balls for industrial applications, consider:
– Alumina content (typically 23%, 65%, or 92%)
– Size and diameter specifications
– Bulk density requirements
– Specific surface area needs
Keyword: inert ceramic ball
– Operating temperature range
– Chemical compatibility with process media
## Maintenance and Handling
Proper handling ensures optimal performance:
– Clean storage conditions
– Careful loading procedures
– Regular inspection for wear
– Proper cleaning methods
– Appropriate replacement schedules
## Future Trends
The inert ceramic ball market continues to evolve with:
– Development of nano-structured ceramic materials
– Improved manufacturing precision
– Enhanced thermal properties
– Customized solutions for specific industries
– Environmentally friendly production methods
## Conclusion
Inert ceramic balls have become indispensable components in numerous industrial processes due to their exceptional properties and versatility. From petrochemical refining to environmental protection, these high-performance ceramic spheres continue to enable more efficient, reliable, and sustainable industrial operations across multiple sectors.