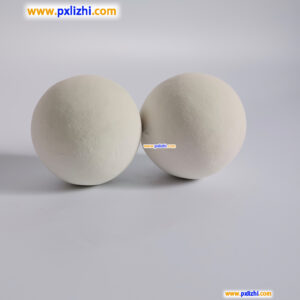
# Inert Ceramic Balls: Key Components in Industrial Applications
## Introduction to Inert Ceramic Balls
Inert ceramic balls are spherical ceramic materials designed to withstand extreme temperatures, corrosive environments, and high-pressure conditions without reacting chemically with the substances they come into contact with. These versatile components play a crucial role in numerous industrial processes where chemical inertness and thermal stability are paramount.
## Composition and Manufacturing
Inert ceramic balls are typically made from high-purity alumina (Al₂O₃), with alumina content ranging from 17% to 99%. The manufacturing process involves:
- Raw material selection and purification
- Precise mixing and forming
- High-temperature sintering (typically 1500-1800°C)
- Quality control and grading
## Key Properties
Why Industries Choose Inert Ceramic Balls
The widespread adoption of inert ceramic balls across industries stems from their exceptional properties:
- Chemical Inertness: Resistant to acids, alkalis, and organic solvents
- Thermal Stability: Can withstand temperatures up to 1800°C
- Mechanical Strength: High crush resistance and wear resistance
- Low Water Absorption: Typically less than 5%
- Uniform Size Distribution: Precise diameter control for consistent performance
## Industrial Applications
Where Inert Ceramic Balls Make a Difference
Petrochemical Industry
In refinery processes, inert ceramic balls serve as:
- Support media for catalysts in reactors
- Distributors for liquid and gas flows
- Heat exchange media in high-temperature applications
Chemical Processing
Chemical plants utilize these balls for:
- Packing material in absorption and distillation columns
- Bed support in fixed-bed reactors
- Corrosion-resistant media in harsh chemical environments
Keyword: inert ceramic ball
Environmental Applications
In pollution control systems, inert ceramic balls:
- Support catalysts in SCR (Selective Catalytic Reduction) systems
- Serve as media in biofilters for waste gas treatment
- Act as heat recovery media in thermal oxidizers
## Selection Criteria
Choosing the Right Inert Ceramic Balls
When selecting inert ceramic balls for specific applications, consider:
Factor | Consideration |
---|---|
Alumina Content | Higher alumina means better chemical resistance and strength |
Size | Diameter typically ranges from 3mm to 50mm |
Operating Temperature | Must match the process temperature requirements |
Pressure Conditions | Higher pressures require higher crush strength |
Chemical Environment | Must be compatible with process chemicals |
## Maintenance and Longevity
Proper maintenance ensures optimal performance and extended service life:
- Regular inspection for cracks or wear
- Proper loading techniques to prevent breakage
- Periodic cleaning to remove deposits
- Monitoring for signs of chemical attack