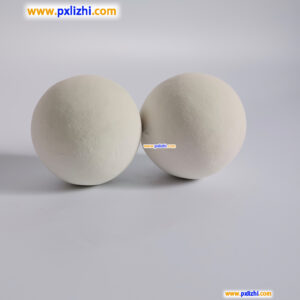
# Inert Ceramic Ball Applications in Industrial Processes
## Introduction to Inert Ceramic Balls
Inert ceramic balls are high-quality, chemically stable ceramic spheres used in various industrial applications. These balls are manufactured from high-purity alumina or other ceramic materials, offering excellent resistance to heat, corrosion, and mechanical wear. Their inert nature makes them ideal for processes where chemical reactivity must be minimized.
## Key Properties of Inert Ceramic Balls
Keyword: inert ceramic ball
The effectiveness of inert ceramic balls in industrial processes stems from their unique characteristics:
– High temperature resistance (up to 1600°C)
– Excellent chemical stability
– Low water absorption
– Superior mechanical strength
– Resistance to thermal shock
– Uniform size and shape
## Major Industrial Applications
### 1. Catalyst Support in Petrochemical Industry
Inert ceramic balls serve as excellent catalyst supports in petroleum refining and petrochemical processes. They provide:
– Structural support for catalyst beds
– Even distribution of reactants
– Protection against catalyst crushing
– Improved heat transfer
### 2. Packing Material in Chemical Towers
These ceramic balls are widely used as tower packing in distillation, absorption, and stripping columns:
– Create uniform vapor/liquid distribution
– Increase mass transfer efficiency
– Reduce pressure drop
– Prevent channeling effects
### 3. Grinding Media
In the ceramics and paint industries, inert ceramic balls function as grinding media due to their:
– High density
– Wear resistance
– Contamination-free grinding
– Consistent particle size reduction
### 4. Heat Storage Mediums
Some high-temperature industrial processes utilize inert ceramic balls for thermal energy storage:
– Store heat during peak production
– Release heat during low production periods
– Maintain consistent process temperatures
– Improve energy efficiency
## Selection Criteria for Industrial Use
When choosing inert ceramic balls for specific applications, consider:
– Alumina content (92%, 95%, or 99%)
– Size and diameter specifications
– Bulk density requirements
– Crushing strength needs
– Operating temperature range
– Chemical compatibility with process media
## Maintenance and Handling
Proper handling ensures optimal performance and longevity:
– Clean surfaces before installation
– Avoid sudden temperature changes
– Inspect regularly for breakage
– Replace damaged balls promptly
– Store in dry conditions
## Future Trends in Application
The use of inert ceramic balls continues to expand with:
– Development of nano-structured ceramic materials
– Applications in renewable energy systems
– Advanced catalytic processes
– High-efficiency heat recovery systems
As industrial processes become more sophisticated, the demand for high-performance inert ceramic balls with specialized properties is expected to grow significantly.