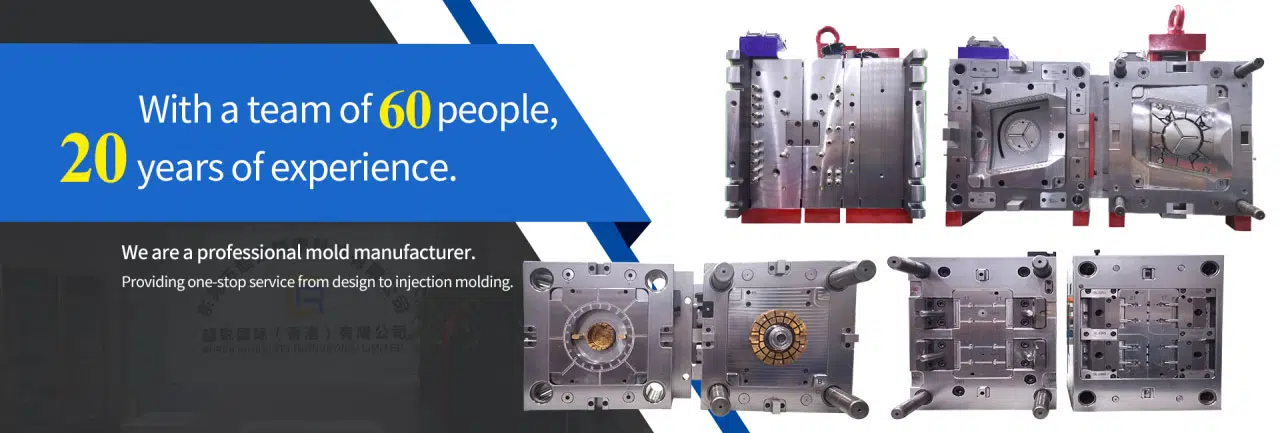
# Vacuum Casting Technology in Modern Manufacturing
## Introduction to Vacuum Casting
Vacuum casting is a versatile manufacturing process that has gained significant popularity in modern production environments. This technique combines the precision of traditional casting methods with advanced vacuum technology to create high-quality parts with excellent surface finishes and dimensional accuracy.
## How Vacuum Casting Works
The vacuum casting process begins with the creation of a master pattern, typically made using CNC machining or 3D printing. This pattern is then used to create a silicone mold under vacuum conditions to ensure no air bubbles are trapped in the mold material.
Once the silicone mold is prepared, the casting material (usually polyurethane resin) is poured into the mold while maintaining the vacuum environment. This vacuum-assisted pouring ensures complete filling of even the most intricate mold details without any air entrapment.
## Advantages of Vacuum Casting Technology
Vacuum casting offers several compelling benefits for modern manufacturers:
Keyword: Vacuum Casting
– Cost-effective for small to medium production runs
– Excellent reproduction of fine details
– Wide range of material options with different properties
– Faster turnaround compared to traditional manufacturing methods
– Ability to produce parts with properties similar to injection-molded components
## Applications in Various Industries
This technology finds applications across multiple sectors:
### Automotive Industry
Manufacturers use vacuum casting for prototyping interior components, light covers, and various functional parts before committing to expensive production tooling.
### Medical Device Manufacturing
The medical field benefits from vacuum casting’s ability to produce sterile, biocompatible components with complex geometries for surgical instruments and diagnostic equipment.
### Consumer Electronics
Many electronic device housings, buttons, and connectors are first prototyped using vacuum casting before mass production.
## Material Options in Vacuum Casting
Modern vacuum casting systems can work with various materials that mimic the properties of:
– ABS-like resins
– Polypropylene-like materials
– Transparent and flexible polyurethanes
– High-temperature resistant compounds
– Flame-retardant formulations
## Future Developments in Vacuum Casting
As manufacturing demands evolve, vacuum casting technology continues to advance. Researchers are working on:
– New resin formulations with enhanced mechanical properties
– Improved automation in the casting process
– Integration with digital manufacturing systems
– Environmentally friendly material options
– Faster curing technologies
## Conclusion
Vacuum casting has established itself as a crucial technology in modern manufacturing, bridging the gap between prototyping and mass production. Its ability to produce high-quality parts quickly and cost-effectively makes it an invaluable tool for product development across numerous industries. As materials and processes continue to improve, vacuum casting will likely play an even more significant role in the manufacturing landscape of the future.